In giro per l’azienda a cercare attrezzi e informazioni
Il paradosso sta tutto dentro un numero: il 15. Nonostante si lavori in meno di due metri quadrati, ogni giorno si rischia di andare avanti e indietro per l’azienda per 15 chilometri. È lo spazio che si rischia di coprire passo dopo passo per recuperare materiali, attrezzi, componenti o per chiedere istruzioni e informazioni. Spesso aspettando risposte di altri. Quanto tempo perso. Un’altra risorsa sprecata. E gli sprechi aziendali, spesso senza rendersene conto, sono nascosti dentro a ogni funzionalità dei processi produttivi. Con un’aggravante: questo capita quando il lavoro dell’uomo non viene messo al centro.
È bastato montare una bicicletta in legno secondo due metodi diversi – tradizionale e innovativo - di organizzazione e degli spazi di lavoro per misurare la differenza: produttività aumentata fino al 30%; taglio dei tempi finali di set up fino al 45%, triplicato il numero dei pezzi montati nello stesso tempo. È competitività recuperata. «Oggi il tempo è una risorsa scarsa, è indispensabile dare più attenzione allo spazio di lavoro, alla sua organizzazione e alle persone. Credo sia una reale opportunità anche per far emergere talenti che si hanno in azienda».
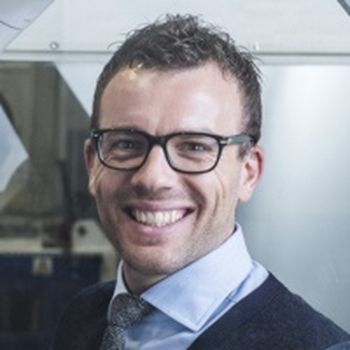
Presidente Nts di Lallio
C’è soprattutto lui, Marco Manzoni, titolare della Nts di Lallio, 250 dipendenti, azienda familiare in senso stretto e leader nella progettazione e produzione di stampi e stampaggio di articoli in materiale plastico, seduto nella stessa aula il giorno dell’inaugurazione formale dell’Academy dell’azienda. È lo sforzo di Nts di rendere la formazione interna ancora più una costante, capace di rispondere alle necessità dell’azienda e delle persone. «Sono investimenti per elevare la professionalità di ciascuno e il benessere sul lavoro. Dobbiamo avere in testa – spiega Manzoni - che c’è sempre un modo migliore per fare le cose rispetto a quanto fatto ieri: è “il sale” di chi si impegna a rendere ancora sostenibile la produzione industriale». È anche il giorno in cui Nts ha deciso, nel suo 60esimo anno di attività, di dare una svolta e adottare un proprio modello organizzativo, su misura. Dall’altra parte, la consulenza della società specializzata EY. Si parte con una esortazione: «Utilizzando le mani si riesce a cogliere al meglio l’ottica della lean manufacturing» annuncia Massimo Trebesca, operation manager di EY. Sono le due parole magiche della giornata: lean (snella) e manufacturing (produzione).
Il metodo è secco, origini e sigle giapponesi, la Toyota modello di assoluto riferimento come fabbrica lean. Anche per aver insegnato la logica di questo metodo: non si adotta solo per tagliare sprechi, sovrapproduzione, tempi morti, perdite di processo, scorte. «Standardizzare un processo di lavoro – ha spiegato Manzoni – significa darsi una priorità irrinunciabile: certificare lo standard di sicurezza».
Taglio di sprechi, tempo e risorse: produttività a +15%
Calare il metodo lean in una di fabbrica reale. Per misurare subito i risultati. Significa prendere nuove distanze su spazi, tempi, processi e anche sulle persone. Vuol dire cambiare l’approccio a concetti come innovazione che richiedono processi rapidi e l’impegno spesso di una sola parte degli uomini di un’impresa. Il metodo Lean, calato in un’azienda vera, richiede un’altra visione. Viaggia per miglioramenti continui, lenti ma costanti. Richiede un coinvolgimento di tutti i collaboratori. «Funziona se si riescono a portare “a bordo” le persone. E solo se spieghi loro il perché, se non è una scelta calata dall’alto. L’essenza è coinvolgere i collaboratori per far capire che cosa si sta costruendo». Ed è merito di questa ampia condivisione del metodo se si registrano piccoli, ma continui progressi organizzativi e di efficienza». Marco Manzoni, patron della Nts di Lallio, controlla i risultati registrati dopo quasi due mesi di applicazione del metodo lean in azienda. Il primo indicatore dice che in un solo mese sono stati abbattuti gli sprechi fino al 15% per ogni ordine di lavoro. Anche questo è un dato di recupero di produttività e di competitività. Manzoni lo spiega così, premettendo che «siamo in continua implementazione del programma e c’è ancora molta strada che dobbiamo fare».
Nel dettaglio, invece, Manzoni spiega che «in azienda stiamo già applicando il cosiddetto “metodo Smed”, fa parte del percorso lean production e punta alla riduzione dei tempi di setup, i tempi di cambio produzione. Questo primo approccio lo abbiamo applicato per gli attrezzaggi stampi. Mentre i cinque principi pilastro, le famose “5S”, cuore della vera metodologia lean, invece, l’abbiamo applicata in tutti i reparti produttivi. I risultati non si sono fatti attendere: abbiamo già registrato – spiega Manzoni - la riduzione degli sprechi fino al 15% per ogni ordine di lavoro».
Almeno quattro sono state le direttrici lungo le quali la Nts ha ridefinito specifici interventi di revisione organizzativa ottenendo un incremento di valore. Su questi aspetti il registro di Manzoni è estremamente dettagliato. «Il primo intervento si è fatto per ridurre proprio le perdite di tempo nel cercare attrezzature e strumenti. Significa minori spostamenti “a vuoto” delle persone: abbiamo calcolato che alla fine di tutto questo muoversi inutilmente si traduceva in vere e proprie “maratone” di ore e km tutto dentro l’azienda». Lo slogan è indicativo di questo risultato: un posto per ogni cosa, ogni cosa al suo posto. Ordine, presenza dei soli materiali necessari, una loro nuova movimentazione e spazi più liberi hanno fatto il resto.
Ma ancora più determinanti sono stati gli interventi per ridurre i fermi macchina dovuto al miglioramento dei tempi del setup: elaborazione di un nuovo flusso di produzione e una sua maggiore sincronizzazione sono stati il primo passo. E che ci porta diritti al terzo giro di boa:la riduzione degli errori di lavoro. «Ripensare procedure e istruzioni per farle rientrare in un modello standard è determinante – spiega Manzoni –, aiuta a ottenere la più ampia condivisione degli stessi passaggi e procedure fra le diverse squadre di lavoro che si alternano in produzione. Tutti adottano gli stessi criteri e uguali procedure». E poi meno tempo perso a chiedere in giro «come si fa». Anche perché ora in Nts le informazioni sono ben visibili in ogni reparto della produzione: strumenti sia visual sia digital, sia su carta sono evidenti in tutte le zone comuni e a disposizione dei lavoratori.
talk
Perché avete deciso di affrontare questa svolta?
<p class="risposta-print">Il tema Lean in azienda è sempre più presente con l’obiettivo di incrementare la produttività (e farlo in modo sicuro ed ergonomico perché non c’è vero miglioramento senza la forte attenzione al lavoratore) insieme al valore offerto al cliente. Concetti come il miglioramento continuo devono andare di pari passo con l’ordine, la pulizia, la standardizzazione e soprattutto il coinvolgimento e la motivazione delle persone.<br/></p>Il metodo è stato adottato. Quale sarà il prossimo passo?
<p class="risposta-print">Faremo un assessment ancor più dettagliato di tutti i processi aziendali, non solo quelli produttivi ma anche quelli di ufficio (Lean office), per implementare l’approccio Lean ovunque e continuare la nostra lotta agli sprechi.<br/></p>Qual è allora il vostro sogno finale?
<p class="risposta-print">Lo spreco non è solo funzionale alla riduzione di costi dell’azienda (che significa anche ottimizzazione delle risorse come le materie prime, energia elettrica, ecc.), ma anche al miglioramento della qualità del lavoro della persona che lavora meglio e con più efficienza. Il sogno? Arrivare al World Class Manufacturing.</p>Il metodo lean in 5 mosse e in «chiave» giapponese
Ecco le che cosa rappresentano in una logica Lean le «5S» che ne costituiscono le regole portanti. Partendo dalla prima considerazione, forse la più importante che induce ad adottare il metodo Lean. È una regola che non rientra fra queste famose «5S». Ma è sicuramente il primo obiettivo che si ottiene garantendo una perfetta organizzazione del lavoro: la sicurezza sul e del posto di lavoro. Ordine e pulizia sono i capisaldi di questo approccio.
Ecco che cosa signifcano:
1 - «Seiri», ovvero separare le cose utili da quelle che creano sprechi
Si inizia individuando le cose e i processi utili, isolando quelli inutili. Se un processo può essere eliminato senza conseguenze sulla produzione e sulla qualità del processo di lavoro, eliminalo.
2 - «Seiton», ovvero ordinare
Procedere quindi con il progetta ilo spazio di lavoro in modo tale che tutti possano facilmente raggiungere tutto ciò di cui hanno bisogno e che tutti i materiali e tutti i prodotti in lavorazione possano effettuare il loro percorso in modo lineare ed efficiente.
3 - «Seiso», ovvero pulire
Un posto di lavoro pulito è un posto di lavoro che permette la piena efficienza. Prendersi cura del proprio posto di lavoro significa anche riconoscerne il valore.
4 - «Seiketsu», ovvero standardizzare
All’interno dello spazio di lavoro, fai in modo che le procedure siano standardizzate e rese efficienti, assicurati che ogni lavoratore possa avere chiare le operazioni che deve svolgere e le lavorazioni delle quali è responsabile, avendo subito a disposizione tutto ciò che gli serve.
5 - «Shitsuke», ovvero sostenere
Fare in modo che questi principi vengano compresi, condivisi e applicati da tutti i lavoratori. Proprio così, non si parla di obbedienza, ma di condivisione: un valore fondante della strategia Lean .