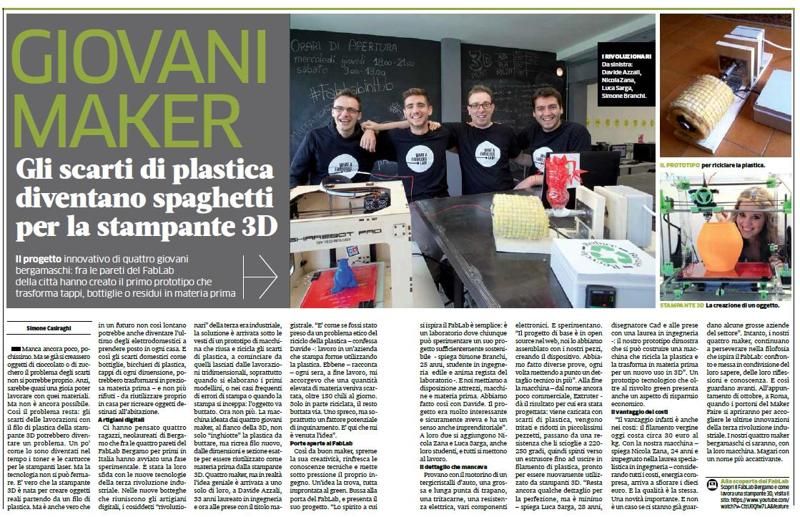
Ecobergamo / Bergamo Città
Sabato 28 Giugno 2014
Gli scarti di plastica
spaghetti in 3D
Gli scarti domestici come bottiglie, bicchieri di plastica, tappi di ogni dimensione, potrebbero trasformarsi in preziosa materia prima – e non più rifiuti - da riutilizzare in casa per ricreare oggetti proprio per l’abitazione.
Gli scarti domestici come bottiglie, bicchieri di plastica, tappi di ogni dimensione, potrebbero trasformarsi in preziosa materia prima – e non più rifiuti - da riutilizzare in casa per ricreare oggetti proprio per l’abitazione.
Ci hanno pensato quattro ragazzi, neolaureati di Bergamo che fra le quattro pareti del FabLab Bergamo per primi in Italia hanno avviato una fase sperimentale e sfidare il tema. Nelle nuove botteghe che riuniscono gli artigiani digitali, i cosiddetti “rivoluzionari” della terza era industriale, la soluzione è arrivata sotto le vesti di un prototipo di macchina che riusa e ricicla gli scarti di plastica, a cominciare da quelli lasciati dalle lavorazioni tridimensionali, soprattutto quando si elaborano i primi prototipi, o nei casi frequenti di errori di stampa o quando la stampa si inceppa: l’oggetto va buttato.
Ora non più. La macchina ideata dai quattro giovani maker, al fianco della 3D, non solo “inghiotte” la plastica da buttare, ma ricrea filo nuovo, dalle dimensioni e sezione esatte per essere riutilizzato come materia prima dalla stampante 3D. Quattro maker, ma in realtà l’idea geniale è arrivata a uno solo di loro, a Davide Azzali, 33 anni laureato in ingegneria e ora alle prese con il titolo magistrale. Da buon maker, spreme la sua creatività, rinfresca le conoscenze tecniche e mette sotto pressione il proprio ingegno. Un’idea la trova, tutta improntata al green.
Bussa alla porta del FabLab, e presenta il suo progetto. “Lo spirito a cui si ispira il FabLab è semplice: è un laboratorio dove chiunque può sperimentare un suo progetto sufficientemente sostenibile - spiega Simone Branchi, 25 anni, studente in ingegneria edile e anima di regista del laboratorio -. E noi mettiamo a disposizione attrezzi, macchine e materia prima. A loro due si aggiungono anche Nicola Zana e Luca Sarga, anche loro studenti, e tutti si mettono al lavoro.
Alla fine la macchina – dal nome ancora poco commerciale, Extruter - dà il risultato per cui era stata progettata: viene caricata con scarti di plastica, vengono tritati e ridotti in piccolissimi pezzetti, passano da una resistenza che li scioglie a 220-250 gradi, quindi spinti verso un estrusore fino ad uscire in filamento di plastica, pronto per essere nuovamente utilizzato da stampanti 3D.
© RIPRODUZIONE RISERVATA